What’s inside:
Today we delve into the intricacies of managing hospital inventory, focusing on consignment arrangements and implant tracking.
Dive into our insights, including:
- What is consignment inventory management
- The importance of implant tracking systems for consigned stock
- Compliance and regulatory considerations
- Supply chain optimization techniques
Consignment inventory management is a common cause of disputes. Today I’m looking at 5 common consignment conflicts between vendors and providers – and how to solve them.
If you’re spending way too long investigating data disagreements, then it’s time to break free from a cycle of poor hospital supply chain processes. Now is the time to use technology to add trust and transparency to vendor managed inventory (VMI).
5 common sources of consignment inventory disputes
Consignment management often involves time-consuming liaison between vendors and healthcare facilities, as they endeavor to reconcile their consignment inventory issues and come to agreement on stock levels, procurement and billing.
Let’s take a look at 5 common challenges that regularly trigger trouble between supply chain partners.
1. Inefficiencies of manual consignment inventory management
Vendors often struggle to maintain accurate records of inventory stored on hospital sites. This vendor managed inventory (VIM) is often manually managed, and prone to counting errors and delayed updates.
Manual processes can leave all parties unclear on actual inventory levels, fueling misunderstandings on which stock items are actually available or require restocking. Manual implant tracking is an outdated, labor-intensive method for monitoring and managing consignment inventory and the lack of accurate, real-time data is a common cause of disputes.
With limited inventory visibility and off-site management by vendors, it’s hard to gain real-time data and ensure timely restocks of all items, so that the staff have the right products available upon demand.
2. Addressing data discrepancies for consignment inventory
Vendors and hospitals often work with separate inventory management systems – sometimes automated systems, other times just spreadsheets. These different inventory tracking methods often lead to two sets of disparate data, making it challenging to reach agreement on the current situation and the action required. For example, if there is no clarity on stock levels, then it is difficult to agree restock requirements.
When fundamental data can’t be relied up, the delay to decision making on vital operational activities can lead to billing disputes and disagreements but can also affect the availability of inventory and the delivery of high-quality patient care.
Providers and vendors are increasingly turning to automated inventory management technology to support a more unified way of working.
3. Expiry management of consignment stock
Consignment chain of custody agreements provide clarity on the transfer of custody of consignment inventory from one party to the other. It covers legal and regulatory accountability and liability.
In terms of expiry management, a typical agreement gives vendors responsibility for managing consignment inventory levels and replenishment, and overseeing stock control, as well as expiry and recall management.
Vendors must ensure that consignment stock is regularly rotated to prevent items from expiring on the shelves in order to prevent unnecessary wastage costs. Even more crucial, is the issue of expired products being left on the shelves, which can damage the vendor’s reputation and present a patient safety risk.
Ultimately, the hospital needs to trust that the consigned products provided are safe to use and don’t expose them to risk of accidental usage.
The hospital needs to ensure it meets it regulatory compliance criteria, and as consignment inventory only becomes the responsibility of the hospital at the point of use, it is best practice to put procedures in place to ensure every item is safety-checked before usage, rather than relying on the vendor’s scrutiny alone.
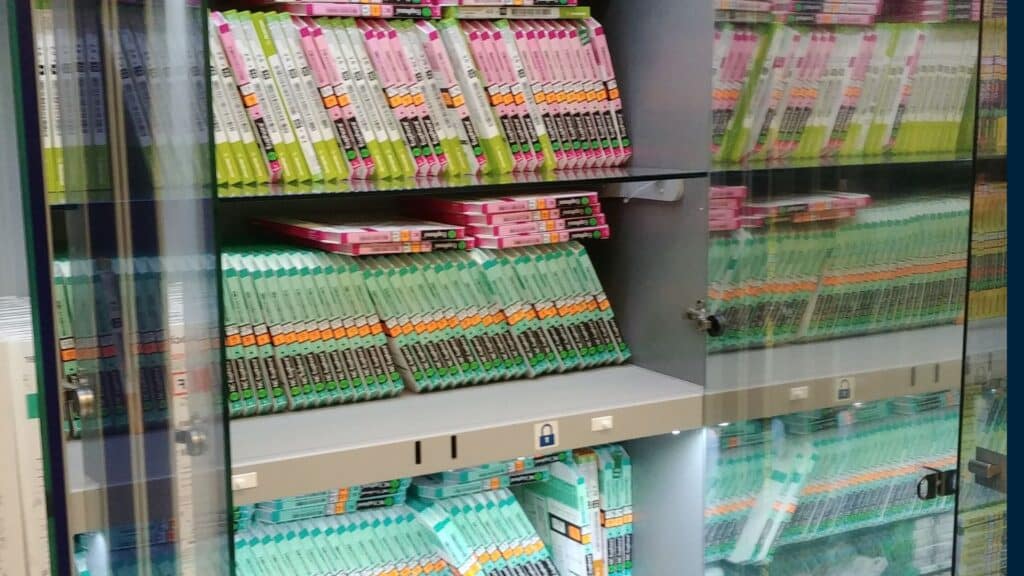
4. Liability for loss or damage:
Liability for loss or damage is a critical aspect of consignment stock management and can often lead to conflicts between providers and vendors. Disputes may arise over whether the loss occurred during transportation, storage, or handling. Additionally, issues such as inadequate packaging, improper handling procedures or unsecure storage facilities can further complicate liability assessments.
Establishing clear accountability, agreeing risk management strategies, and taking steps to mitigate risks is important in preventing these conflicts.
When automated implant tracking systems are used, the added security and efficiency provide greater clarity on this issue.
5. The cost of data reconciliation and dispute resolution with vendor managed inventory
Reconciling conflicting vendor and provider consignment data can be a resource and time-intensive process. The inventory counts, documentation reviews, plus faxes, emails and calls between both parties may ultimately lead to agreement on the data but it diverts resources from other key tasks and can put a strain on working relationships.
Inefficient consignment inventory systems certainly carry a cost.
For a system to run smoothly there needs to be real time visibility, accurate data and shared vision. Without these three key elements both parties are set up to fail.
We can see that the management of consignment inventory presents numerous challenges and complexities for both vendors and providers. Looking at these five common causes of consignment conflicts demonstrates the need to have strong protocols and systems in place.
The best and most common solution to consignment conflicts is to use a single, automated implant tracking system, which provides access to all parties.
Consignment inventory management solution
Automated smart cabinet technology is providing a central source of data for providers and vendors. RFID tracking with cloud management software enables multiple parties to access the same core data, ensuring everyone has shared and accurate vision of consignment inventory.
An RFID smart cabinet automatically tracks consignment stock, and the managing software is able to provide real-time metrics, reports and analytics. This vital data ensures everyone is clear on stock levels and usage and can use data insights for smarter planning and management.
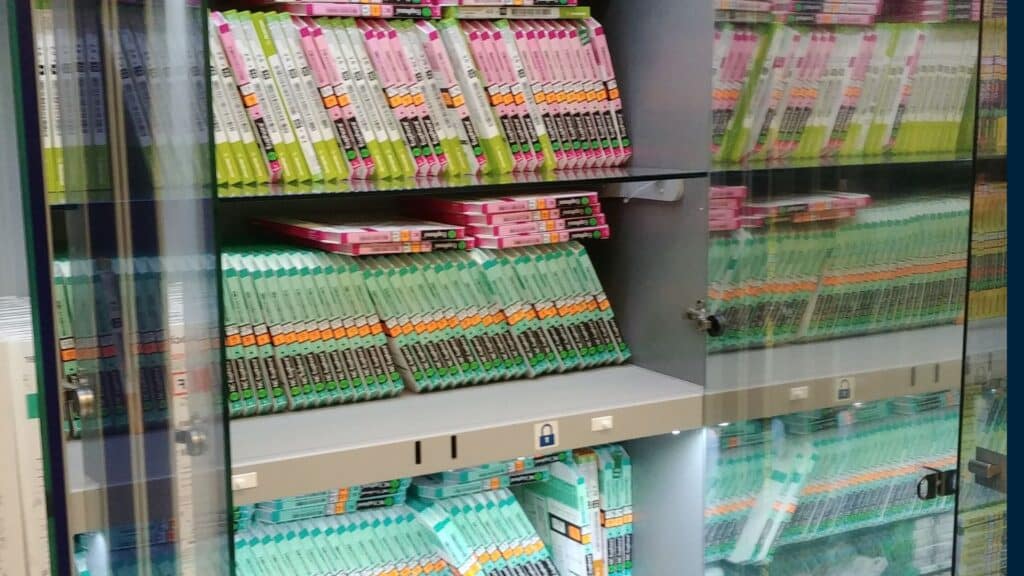
TotalSense RFID smart cabinet solution for consignment management
IDENTI’s TotalSense RFID smart cabinet is often used by customers as a consignment management system.
It provides automated tracking and real-time visibility for ALL supply chain partners – ensuring everyone is in complete agreement on inventory data. Full visibility and a shared understanding of stock levels leads to timely restocks. Automated expiry management reduces expiry wastage to zero and ensures all items are safety-checked.
TotalSense provides the real-time data and shared inventory vision that makes vendor managed inventory simple to oversee.
Once all parties share a common understanding this enhances performance, supports data-driven decision making and makes contract monitoring simple.
With a central resource providing clear, accurate data to all parties, finally trust and transparency are achieved, putting an end to disputes.
Contact me if you want more information on a stress-free consignment management system, that puts all parties are on the same page.