What’s inside:
The FDA UDI regulations are established in US hospitals and ambulatory centers, who have put systems in place to support regulatory compliance.
However, orthopedic kits, sets and trays remain problematic to document and recording the UDI details of non-sterile implants on the EMR is a common challenge.
This e-book examines:
- The importance of UDI implant tracking of orthopedic medical inventory
- Why non-sterile kits, sets, trays and implants are hard to track.
- How technology can provide an orthopedic point of use data capture solution
FDA UDI Regulations and orthopedic tracking
The FDA introduced Unique Device Identification (UDI) to provide a global standard for the identification and tracking of medical devices.
The UDI system involves a consistent data structure being used to identify each product.
Once a device is labelled with a UDI barcode, end-to-end implant tracking is possible – from manufacture through distribution, delivery, storage and usage.
Using a standardized identifier means that the item is visible across different organizations – manufacturer, vendor, distributor, distribution center, healthcare provider.
The UDI system facilitates accurate item tracking, right through to consumption. This information is then shared with hospital systems to:
- Protect patient safety
- Improve inventory management
- Facilitate medical billing
However, due to the need to sterilize orthopedic kits and trays, which involves the removal of the packaging and therefore detachment of each item from its UDI, this type of medical inventory remains problematic to record during surgery.
UDI and Patient Safety
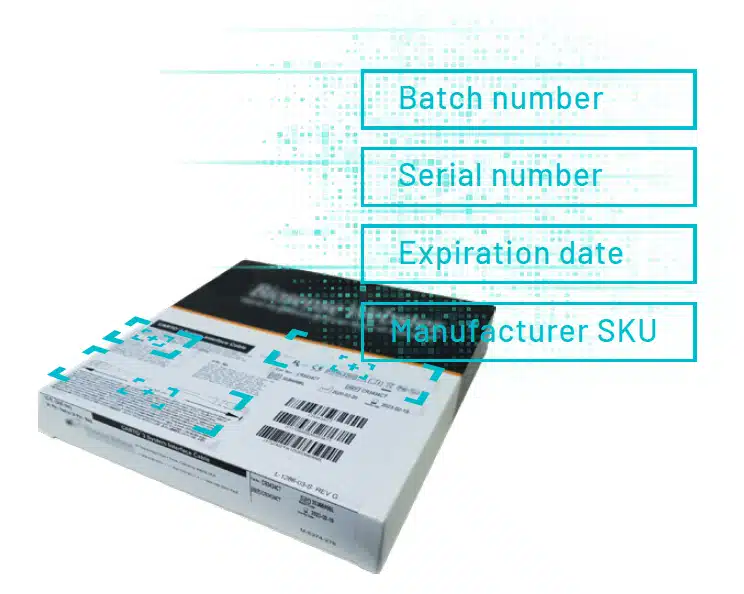
One of the most important benefits of UDI tracking is the digital link made between implants and patients.
At the point of care the Circulating Nurse records the UDI of medical devices and implants onto the patient’s electronic medical record (EMR). This ensures that, should a future product recall occur, the patient can be quickly tracked and traced.
The Allergan breast implant recall from 2019 was a wake-up call for the healthcare industry, when tens of thousands of women who received the implant could not be traced. This reinforced the importance of digitally documenting implants.
The documentation of consumption is probably the most vital step of UDI implant tracking, as it safeguards patients.
UDI provides a digital link between products and patients.
Implant Management
As medical devices and implants can be expensive, it is important for healthcare providers to achieve full visibility and control.
Automated inventory management systems consist of hardware and software, with the best systems providing real-time metrics, useful reports and insights.
Automated implant tracking ensures that:
- Materials management gain real-time vision of stock levels
- Effective and timely expiry and recall management can be achieved, reducing wastage and safeguarding patients.
- Usage data informs accurate restocks
- Full FDA UDI compliance is achieved
Automation adds accuracy to the inventory management process, and this reduces costs.
However, it’s not just costs that need to be controlled – it’s reimbursement too.
Optimal revenue is dependent on the device identifiers of all billable items, being captured at the point of care.

Recouping the cost of high-value implants
Hospitals and ASCs are complex organizations that can carry hundreds of thousands of stock items.
Medical Supply Costs (2018 figures)
- Medical and surgical supply costs average $27.4 million a year, per hospital.
- This will rise to $44 million a year, if growth continues at the same rate.
- In total it is estimated that U.S. hospitals spent around $200 billion on medical devices.
Relationship between reimbursement and UDI
In order for billable items to be reimbursed they need to be fed into the charge capture system.
At the point of care, it is the UDI code that is used to identify and chart the item, and this data is then shared with other departments, eg. Billing, Claims.
Different types of medical inventory
There are different types of stock, and organizations need to have systems in place to digitally document all of these items.
– General supplies
– Medical devices and implants
– Last-minute items
– Consignment
– Kits and trays
Stock items are those which have been processed by Central Supply and are on the hospital ERP.
When items are pre-loaded onto the system it should be a simple job to identify the item using its UDI information. However, care still needs to be taken, as barcode scanning doesn’t always collect all the data required, such as the expiry date or batch number – and this then needs to be manually keyed in.
Non-stock items are not on the system and could be last minute stock, bill-only items or consignment. They may also include stock items that were substituted by the vendor and didn’t make it onto the system.
Non-stock items are more difficult to record.
UDI Data Capture
Item Capture
Medical devices and implants arrive at the hospital and are loaded onto the ERP system.
The best way to store these stock items is in an RFID cabinet, which can automate the tracking of medical devices and implants. These cabinets are able to report on their current stock levels, as well as log when individual items were removed.

At the point of use, the item will again need to be tracked. To do this it will need to be recorded on the patient’s chart. Nurses often report difficulties charting usage, eg. due to scanning or system issues.
Some types of medical supplies need careful attention, eg. bill only items or consignment – which are outside of hospital systems and so cannot be immediately recorded.
Items that are not routinely recorded during surgery risk not being documented at all.
What makes non-sterile implants difficult to record?
Non-Sterile implants may be hospital-owned (stock), loaned or consignment.
Stock items are generally delivered unsterile from the manufacturer and are either received by hospital Central Supply or may go straight to the Sterile Processing Department (SPD).
These supplies tend to consist of numerous small items that are stored in trays (or sets) and can number hundreds of items. The whole try will get sterilized in one go, before being added to a case cart for delivery to surgery.
The UDI challenge for sets and trays is that items are removed from packaging when placed on the tray,
meaning that each product is separated from its UDI label.
The physician will select the items needed from the tray and these then need to be entered onto the system by the Circulating Nurse.
The difficulty in digitally recording nuts, bolts and screws means that, in some cases, electronic documentation is simply not achieved.

GS1 White Paper: ‘Non-Sterile Orthopedic Implants & UDI Capture’
GS1 is a UDI Issuing agency that created the GS1 standards in healthcare which incorporates the UDI regulatory requirements and helps healthcare supply chain stakeholders to implement UDI.
In 2018 they published a white paper, ‘Non-Sterile Orthopedic Implants & UDI Capture‘, which detailed the challenges presented by non-sterile implants in relation to UDI tracking.
Their findings included:
- Identifying the correct barcode to scan on packaging needs to be made easier for nurses.
- The patient needs to be the primary focus for the nurse, so data capture must be simplified.
- If barcode scanning doesn’t work first time, then nurses revert to manual recording, which is slow and error prone. Some items end up not being recorded at all. It was recognized that barcode readability needs to be improved.
- Scanning issues may be barcode related but could also be due to the IT system, the data, system integration or the Item Master.
GS1 Orthopedic Barcode Problems
The GS1 Working Group identified three main issues relating to barcode readability:
- Absence of data: Many Item Masters focus on items that are routinely used and do not store data on all products. Scanning will fail if the UDI number is not on the Item Master.
- Lack of system integration: Without integration between the EHR, ERP and supply chain systems data availability and quality are compromised.
- Lack of data governance processes: OR systems tend not to have built-in reconciliation processes to handle data quality issues that would enable unrecognized items to be retroactively added, edited or marked as an exception on the Item Master. Without this process being in place, when a scanning issue occurs it is not routinely fixed, so when the same item is scanned again in the future it will still not be recognized.
The Working Group urged the industry to seek technical solutions to the challenge of documenting non-sterile orthopedic implants.
So how can technology be used to the UDI item tracking of orthopedic medical devices?
Technology solution for the recording of non-sterile implants
Since the GS1 Working Group, the problem has persisted, without a simple, all encompassing solution that is suitable for:
- implants from a range of manufacturers
- stock items and non-stock items
Barcode scanners and other solutions continue to be widely used to collect data at the point of care. Frustrated Circulating Nurses are still resorting to manual keying-in after scanning fails or doesn’t record all information.
It’s time to think differently.
We need a new approach.
Orthopedic point of use data capture is a vital task, and we need to make this as simple as possible for busy Circulating Nurses, who need to focus on patients not products.
At IDENTI Medical we get it.
And so, we have designed a solution that uses patented image recognition technology. This new tool effortlessly captures, identifies and documents full orthopedic item capture during surgery, including UDI & expiry.
Snap & Go POU computer vision technology
Snap & Go uses patented image-recognition technology and an AI cloud system to document UDI and other key data.

New technology now makes the barcode scanner redundant in the recording of surgical items – and reduces the role of the Circulating Nurse.
Regular items just require a quick ‘snap’ of product packaging to be identified and documented on to hospital systems.
Snap & Go automates the identification of ALL items – even those not on the Item Master such as trunk stock, substitutes and last minute items.
Our POU data capture tool is powered by a managing system that taps into a global SKU database. Each item is quickly identified and then this data is shared with hospital systems so that utilization is documented on the EMR, ERP and MMIS.
Snap & Go: Recording non-sterilized implants
While the quick and simple solution is great for items still in their packaging, it is also an ideal solution for items from orthopedic kits and trays.
Any point of use data capture tool needs to ensure the automatic tracking of orthopedic implants and medical devices used in surgery.
And that’s exactly what IDENTI’s new orthopedic point of use data capture solution achieves.
Snap & Go is able to digitalize hand-written implant sheets.
Nurses simply log the volumes of individual consumables used in surgery – all the hospital-sterilized implants that are taken from the tray. The nurse marks up their implant sheet with the quantities of each item used, and then, at the end of surgery it is a simple task to digitalize this data so that it charts.

Again, the system taps into the global SKU database to ensure identification of each item.
The result?
Full charting of every implant used in surgery, including small consumables which are documented on manual Implant Sheets.
Snap & Go is able to record 100% itemization and charge capture at the point of care.
Snap & Go documents 100% of non-sterilized implants at the point of care
Snap & Go finally provides a surgical data capture solution that takes account of orthopedic medical inventory, including non-sterilized orthopedic items.
Snap & Go is bringing orthopedic point of use data capture into a new era.
Finally, nurses are able to capture 100% of item and charge capture with ease while ensuring full UDI compliance.
Peace of mind at the point of use.

Contact us for more information about Snap & Go data capture tool with implant sheet functionality.