What’s inside:
Upgrading the systems used to manage medical devices and implants can reap big rewards.
We look at three simple health-tech swaps that can transform your implant tracking and medical device management:
- Turning storerooms into virtual smart cabinets
- Swapping POU barcode systems for image recognition technology
- Discovering the power of a virtual item master
It’s time to embrace new technology and recognize its role in achieving a more effective and streamlined implant management experience.
Swap manual counts for a mobile app
Implants stored on the shelves are often manually managed in core area storerooms, but the time has come to ditch inventory counts and replace them with mobile application technology for digital implant tracking.
Why swap to automated storeroom management?
Shifting from a manual implant tracking system releases staff from labor-intensive processes that capture data of questionable quality. Cloud-powered mobile applications can now efficiently scan RFID-tagged implants stored on shelves, creating a virtual smart cabinet in core storerooms.
Many providers use a combination of systems, reserving smart cabinets for their highest-value stock, or sometimes using them solely for consignment management – a common model for French healthcare providers.
Benefits of storeroom automation technology
The mobile application converts a regular mobile device into an RFID scanner, making it simple to introduce automated item management. Using mobile applications for inventory management reduces labor, while increasing the accuracy of item-level tracking.
Real-time visibility:
- Achieves full inventory visibility
- Facilitates easy item location
- Supports improved supply chain management
- Reduces wastage and cuts costs
- Avoids surpluses and stockouts
- Tracks UDI and safeguards compliance
- Improves expiry and recall management
The winning combination of mobile and cloud technology is reshaping the management of implants in healthcare, ensuring prompt, precise data underpins supply chain decision-making.
It’s time to swap the manual monitoring of storeroom implants for automated tracking in the cloud.
Find out more about virtual smart cabinet solutions.
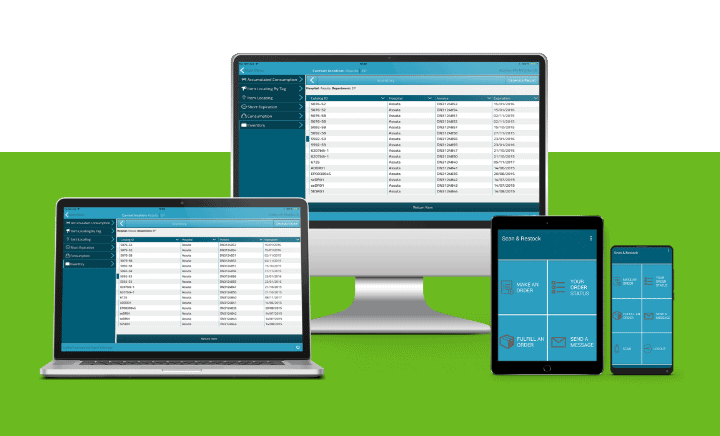
Swap barcodes for image recognition technology
The point of use (POU) is known to be a harsh environment for surgical supply data collection. There are so many factors that complicate the capture of product utilization in surgery – from products that may not be preloaded into the item master, to the failure of barcode technology to capture full item data.
Why swap barcode technology for image recognition?
Traditional systems for POU implant tracking use surgical supply capture systems such as barcode scanners, commonly fail to routinely record every item consumed, and distract perioperative nurses from patient care. Another barrier of barcode systems is all those unboxed products that no longer have a barcode to scan, and loose, non-sterilized items such as orthopedic kits and trays.
The truth is that barcode scanners are only capable of dealing with a subset of the full range of items used in surgery.
A complex range of inventory combined with inadequate point of use technology often results in EHR records that are full of errors and omissions. This is a disaster on three major fronts:
- Clinical records need to be complete and correct
- Medical billing needs to include every item – along with the correct charge
- Supply chain utilization needs to be logged to inform procurement.
In order to ensure the EHR reflects product utilization, and that charge capture is correct, providers often undertake post-surgery reconciliation.
Surely any system that is so ineffective that it regularly requires compensatory activity needs to be replaced!
Luckily there is a custom-point-of-use solution that’s just burst onto the scene. It’s time to chuck out those barcode scanners – POU computer vision tech has arrived!
Benefits of image recognition as a point of use system
Finally, an automated point of use utilization tool that transforms a painful process into a 3 second task. One ‘snap’ of the product under the computer sensor and:
- The package or label is stored as an image
- Full item data is extracted and recorded!
- The screen displays a pre consumption alert for any expired/recalled items
- Products without barcodes can be documented using other information on the packet.
- Handwritten implant sheets can be digitized.
Image recognition, paired with AI technology, is finally putting an end to perioperative paint points, by providing a quick an simple product utilization tool that nurses can rely upon.
It’s time to swap barcode scanners at the point of use for image recognition technology.
Find out more about image recognition POU product utilization technology.

Swap local item master for virtual item master
While we’re still thinking about the point of use, let’s consider all those items that are commonly problematic to record into the EHR – items like:
- Bill-only items, such as trunk stock
- Substitute items
- Items with a revised code that no longer matches the entry in the system
Why swap from a local item master?
These items typically fail when being scanned or entered into the system, and require back-room fixes, or ‘one-time’ entries, in order to record the item on the patient file.
Hospitals struggle to maintain their source of truth, which is used as the reference gateway into their core systems. Because providers switch vendors, change products, and procure items that have dynamic coding, updating the item master is a never-ending task.
So, what if there was a solution that, rather than being updated by one provider, was populated by a global customer base? What if items not listed in the item master were sent for validation into the cloud, and then the provider was given a list of every item that needs to be added or corrected in their local system?
Benefits of a virtual item master
A virtual item master is a SKU database that is accessed and updated by worldwide providers. This system is often adequate to verify every item used, but occasionally there may still be exceptions, and in this case, a human back-office would automatically step in to sort out the issue.
It’s time to swap a local item master for a global cloud-based database.
Find out more about the transforming power of a virtual item master.
The future of implant tracking
Implant tracking is important for patient safety, supply chain management, budget management, operational efficiency and healthcare forecasting.
Healthcare providers who want to ensure the systematic and automated tracking of medical devices, tissue, implants, and other RFID-tagged consumables, need to review their systems.
Things have moved on, and advancements in technology are providing new alternatives that can boost supply chain visibility and tracking overnight. New solutions can streamline workflows, reduce nurse labor and improve both the quality and quantity of item level tracking in healthcare.
These three health-tech upgrades can have a game changing impact on the delivery of healthcare, ensuring optimized patient care and provider performance.
If you want to switch up your implant tracking technology, contact us for ideas and tools.