What’s inside:
Documenting product usage in surgery is a complex task. Although technology has been introduced over the years to automate supply utilization, many of these systems fail to achieve full item and charge capture by the end of surgery.
This white paper looks at the evolution of point of care documentation systems and covers:
- The challenge of documenting supply utilization in surgery
- Feature comparison of different point of use documentation tools
- Digging deeper into the requirements of a point of use (POU) documentation tool
- Feedback from nurses on new tech tool for perioperative documentation
Our latest white paper follows the evolution of point of use surgical supply documentation systems, assessing the effectiveness of each method.
Background
According to the Healthcare Financial Management Association (HFMA), US hospitals lose an average of $1.5 billion a year due to uncaptured usage costs. They also estimate the average OR loss due to supply chain inefficiencies is $1.3 million per hospital.
A contributory factor in both of these issues is poor surgical supply documentation, which costs US hospitals $7.7 billion annually.
Documenting supply consumption at the point of care is vital for efficient supply chain management. Inefficient implant tracking can lead to high wastage costs, inflated supply costs and under-reimbursement, impacting the financial position of healthcare organizations.
Surgical Supply Utilization: The Challenges
Inadequate point-of-use supply documentation systems, longwinded workflows, and nursing non-compliance are common reasons that reportable and billable items are left off the patient file.
This raw OR data is actually vital business information. When the systems in place only capture partial OR utilization, this data gap has a direct impact on management vision and decision making.
New POU technology such as image recognition, AI and machine learning, are providing simpler, more efficient tools that make it easier for nursing staff to record full product usage data in the EHR. The move aware from outdated barcode systems ensures full UDI capture and charting integrity – even for bill-only items, and products arriving into surgery without a barcode.
The cost of getting surgical supply documentation wrong
Perioperative supply documentation faces significant challenges, as revealed by Johnson et al.’s 2018 study, indicating a manual documentation error rate of 11.4% during surgical procedures. Over 85% of nurses and frontline leaders encounter difficulties in accurately documenting supplies used during procedures. A research study in an academic medical center highlighted the substantial time burden on nurses, with the majority spent charting in the EHR (31.63 mins) and reviewing information (21.51 mins), thereby limiting direct patient interaction time.
The repercussions of poor product utilization documentation extend to healthcare costs. Gartner suggests that healthcare organizations could reduce supply chain costs by 5-15% through improved management practices and standardization, emphasizing the importance of accurate consumption data. The HFMA’s findings indicate that US hospitals lose an average of $1.5 billion annually due to uncaptured usage costs. Addressing these documentation challenges becomes paramount for both operational efficiency and cost-saving measures in healthcare settings.
Snap&Go introduces a groundbreaking method for capturing and documenting reportable and billable items in operating rooms (OR) and procedural areas. Using a computer vision sensor, it captures an image of the product label or packet, converting it into data analyzed by AI and machine learning algorithms. The captured data is seamlessly integrated with ERP, EHR, and MMIS systems, ensuring enhanced operational efficiency and supply chain optimization.
This innovative system has profound impacts, providing prompt and accurate consumption data to improve operational efficiency, healthcare delivery, and margins. In the perioperative setting, it enables the achievement of a perpetual inventory, ensuring the availability of the right products when needed, thereby enhancing patient safety and reducing the nurse’s workload.
The power of this data-driven approach is evident in its outcomes, including a 10-20% increase in reimbursement, a 70%+ reduction in waste, 97%+ case cost accuracy, a 30-40% reduction in nurse administrative time, 100% UDI compliance, and a 25%+ reduction in on-hand inventory, demonstrating the tangible benefits of Snap&Go’s comprehensive solution.
Comparing traditional systems with advanced technology
The chart below is based on focus groups and questionnaires, analysis of benchmarks from the industry, qualitative examination of research data and feedback we received from customers in the field. This information was used to draw comparisons between the two technologies.
Current systems | IDENTI’s approach |
Many systems rely on inefficient barcode scanners and manual data entry for data capture. | Image recognition technology captures all data in 3 seconds – whether it’s owned stock, consignment, or a bill-only item. No reliance on barcodes. No more keyed in data. |
Items not preloaded in the system, or where a code change has occurred, are not recognized by the item master and cannot be routinely processed. | Access to a globally-populated item master in the cloud ensures the automated identification of every single item. An exception report is produced for local item master maintenance. |
Patient safety can be compromised by expired or recalled items making it into the OR, risking ‘never events’. | Pre-consumption product validation checks act as the last line of defense in OR, preventing the accidental usage of unsafe items. |
Perioperative nurses are distracted from patient care by clunky systems that make product usage documentation difficult. | Quick and easy item capture, automated product identification, and swift documentation in the patient file, allow nurses to focus on patients, not products. |
Data collected may be incomplete, incorrect and siloed. | Full, accurate, and timely data is shared with core systems. |
Why it’s vital to collect complete and correct OR utilization data
OR data is not just clinical data. It feeds internal workflows for efficient hospital administration and operations and provides vital OR business intelligence.
OR consumption data drives lean supply chain management and has the power to boost organizational performance.
Point of Use Supply Documentation System – Feature Comparison
How efficient are existing systems in dealing with the full range of items that need recording into the EHR, compared to image recognition and AI technology?

DOWNLOAD LINK for comparison infographic: Download the infographic on the Evolution of POU Technology
The Issues POU documentation systems need to get right
Technology
Image recognition, AI and machine learning are modern technologies that are now being applied to healthcare systems and tools. They have advanced capabilities when compared to traditional point of use technology.
Barcode technology can only read items containing working barcodes, and even then, full data may not be extracted.
Item capture
Barcode technology is not reliable at the point of use as it is inefficient at capturing all the required item data and cannot collect data from every type of product used in surgery.
All too often barcode systems lead to data-collection fails, and the nurse is left to fix data, add missing fields, or enter the entire item.
Image recognition technology digitizes an image of product packaging and is not reliant on a working barcode. The full packet is used to compile item data.
Item identification
Traditional point-of-use supply documentation systems reference the local item master as the source of truth, but this can hinder, rather than help, the process of utilization documentation.
Catalog lists are very difficult to maintain as procurement choices vary, and individual item data changes. Even if an item is listed in the local system, the data can quickly become out of date. The reality is that too many items aren’t recognized when entered into the system, driving the process into a manual task, often a ‘one time’ entry.
Snap&Go uses a worldwide item database that gathers information from customers globally and is backed up by human support. This ensures it is perpetually maintained so that every item entered is automatically identified or researched by the back-office team. IDENTI provides customers with a report of all processed items that were missing or incorrectly listed in the local catalog, so that local item master maintenance can take place.
Ease of use
Data collection using barcode technology is hit and miss due to barcode readability issues, incomplete or failed data capture, and reliance on the local item master.
Put simply, data collection can be time consuming, frustrating and inefficient.
Snap&Go achieves quick data capture of all items in just 3 seconds and automates the task of item identification and system documentation. There’s no data fixing, no keyed-in data, no, duplicate entries.
Full and accurate data collection
When data needs to be fixed or entered manually then there is a risk of errors and omissions.
Image recognition and AI technology achieves 100% item and charge capture with speed and ease.
We can compare the technology and tell you the differences, but what do nurses think of computer vision technology at the point of care?
Methodology
Even data companies need the human touch. IDENTI uses customer surveys, focus groups, network meetings and interviews to tap into our healthcare contacts’ and customers’ perioperative documentation challenges, and to gain feedback on our products.
This ‘voice of the customer’ (VOC) research feeds into our product and feature development and design. It ensures that we retain a user focus, with a high emphasis on simplifying workflows while improving data outputs.

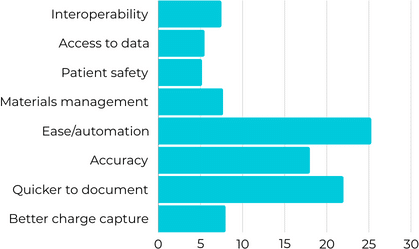
And this is their feedback:
Snap&Go Feature | Nurse feedback on Snap & Go |
Data capture via image recognition technology | “Loved the ease of use. It’s super user friendly and takes the guess work out of putting in supplies or implants.”
“Snaps a picture of ALL information the product, user friendly, less time.” “Saves time, lessens errors.” “Fast, easy, accurate records.” “Quick, easy, error-proof item capture.” |
Data capture of small consumables
(Snap&Go, which can capture and digitize the hand-written implant/count sheets) |
A benefit is recording the “foot & ankle hardware that all comes at the end of the case” |
Automated item identification | “All the information is readily available; no mis–keying in an ID number”
“Complete Data Base of supplies.” |
Digital documentation into hospital systems. | “Actually captures every item used in a surgical procedure accurately.”
“Ease of use and getting all the information into the chart quickly.” |
Charge capture using Snap&Go | One benefit is “capturing more accurate charges.”
“Catches more charges & significant time savings.” “Capturing missing charges that the hospital can use when negotiating insurance contracts to show the true cost of procedures, which could increase the Medicare fee schedule.” |
Patient Safety: More time for patient care | Snap&Go takes the supply chain admin burden off of nurses, allowing them to focus on patients, not products.
A benefit is nurses would “Spend less time doing non nursing things, easier to use.” “Time saving, less possibility of human input error and/or inconsistencies.” |
Patient Safety: Pre consumption safety alerts | Nurses are the last line of defence to prevent the use of unsafe products in surgeries and procedures.
A benefit is, “Catching expired products.” |
Patient Safety: Recall management | “Accurate record keeping and patient safety in event of recalls” |
Interoperability | A benefit is “communication with EPIC and materials.”
“Easy gathering and access to data.” |
Conclusion:
Barcode technology is now outdated and inefficient when compared to the combined power of image recognition, AI and machine learning.
Snap&Go is disrupting the point of use surgical supply documentation market with a next-generation AI tool.
- Reduces nurse supply chain admin at the point of care
- Results in 100% item and charge capture
- Ensures full consumption data for demand-lead procurement.
- Provides data insights that lead to reduced wastage and costs.
- Achieves full charge capture, ensuring optimized RCM and case revenue
Sophisticated data and insights can finally be used for smarter inventory management, optimized billing, enhanced patient safety and compliance.
DOWNLOAD LINK for White Paper: Download the white paper on Supply Utilization at the Point of Care – Traditional Systems v New Tech, to get the lowdown on point of use solutions for recording implant consumption.

Download the full white paper to get all the details: Record Utilization at the Point of Care Using Image Recognition.
About new image recognition technology for point of use supply capture
Snap&Go is a computer vision sensor that is transforming the task of supply documentation in OR and procedural settings.
Breakthrough image recognition technology ensures 3-second item capture, and managing software powered by AI and machine learning algorithms, with access to a global SKU database, ensure that product identification, validation and documentation are completely automated.
This technology is simply the future of perioperative documentation. and is nurse-approved – see perioperative nurse feedback on Snap&Go.

It’s time to join the image-to-data revolution – get in touch to step into the future.