What’s inside:
Documenting product usage in surgery is a complex, frustrating task, mainly due to the inefficiency of existing tools.
Today, we’re looking at how image recognition technology is revolutionizing implant documentation for optimized supply utilization records.
Our video short on the topic gives you a whistle-stop tour, and our article below delves a bit deeper.
Find out:
- The important of a good point-of-use system for tracking consumption
- Why product tracking at the point of care is vital for clinical, operational and management efficiency.
- How barcode scanners have limitations that lead to data inefficiencies
- The role of image recognition and AI technology is simplifying and speeding up utilization in surgery.
Perioperative nurses are responsible for implant documentation at the point of care, ensuring all surgical supplies utilized are listed in the patient file.
The problem is that traditional systems and tools, such as barcode scanners, regularly let them down. For so many reasons:
- Multiple barcodes on packaging make it hard to identify the one they need.
- Data gaps after scanning may require the manual keying in of data such as batch number and expiry date.
- Small, loose items don’t contain barcodes or tags, these unpackaged and untagged items. such as bolts and screws often require data entry and are at risk of being left unrecorded.
- Reliance on the hospital Item Master, which is hard to keep up to date, mean that many items can’t be paired, and therefore can’t be identified or recorded.
- Workarounds and manual data entry add time and frustration to the task, keeping nurses away from direct patient care.
- Many items by-pass enrollment and are delivered direct to surgery, such as trunk stock or bill-only items. These are not on the hospital system and cannot be quickly processed.
Barcode scanning is simply inefficient in the complex OR and procedure room environment.
Luckily new surgical documentation technology is proving to be a gamechanger.
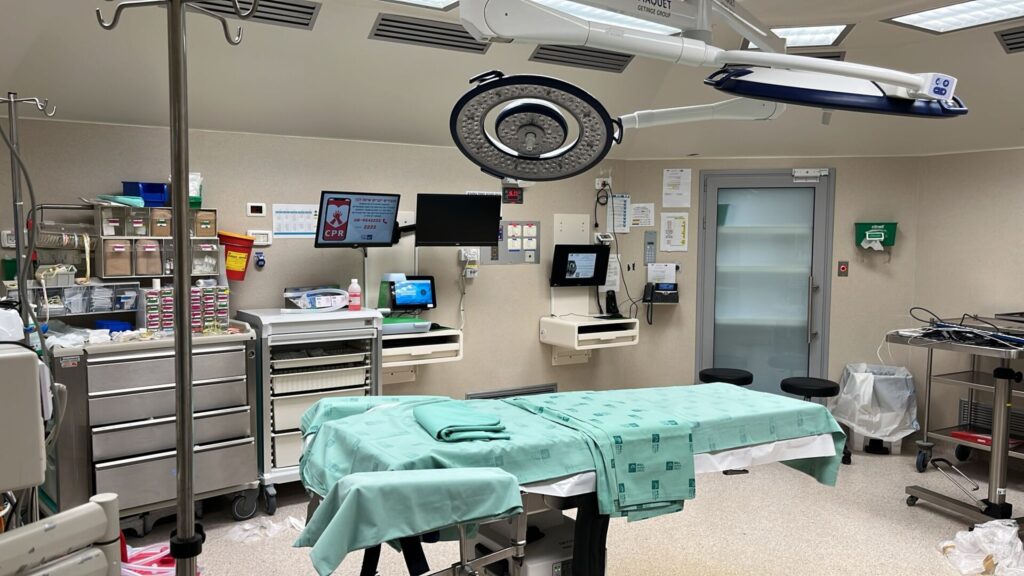
Automated Implant Documentation Process
Snap&Go uses patented image-recognition, AI and machine learning technology to revolutionize the entire process, adding automation and ease of use.
Nurse involvement in supply chain administration at the point of care is minimal using computer vision.
Let’s review the 3-step process to record the products used in surgery, when Snap & Go is used:
1. DATA CAPTURE: This is now a 3 second task.
The nurse places each product under the sensor, and computer vision technology ‘reads’ the full packet, obtaining all the item data that’s required. UDI data is stored ensuring FDA compliance, including tricky data such as batch number and expiry, which commonly need to be manually keyed-in.
2. ITEM IDENTIFICATION: This is now an automated process.
AI technology, machine learning, plus a global product database, all free healthcare organizations from dependence on their Item Master for product identification. With Snap & Go the system taps into the global database to identify each item. If, on the rare occasion, a match can’t be found, our back-office team will handle it all and then load the product into the system for you.
3. USAGE DOCUMENTATION: This is now an automated process.
Snap&Go’s AI software seamlessly shares OR data with the hospital’s EMR, ERP and MMIS.
Prompt, accurate OR utilization data drives through so many operational and administrative processes.
When surgical documentation is made quick and easy, a hospital or ambulatory surgery center can streamline its inventory management, reduce costs, optimize revenue make accurate predictions and data-driven management decisions.
OR product usage data is business intelligence.
Surgical supply documentation is a vital element of healthcare efficiency.
Image recognition and AI technology are proving to be a gamechanger, giving manager full visibility of OR and vital data that supports better decisions.
See our video short on how Snap &Go simplifies surgical implant documentation.
If you want to improve the speed and efficiency of usage documentation at the point of care, let’s talk!
You can check out the product page here.