What’s inside:
Item master match exceptions are a common challenge in healthcare settings. These inconsistencies can lead to significant operational inefficiencies, billing errors, and potentially compromise patient safety.
This article explores the root causes of item master match exceptions and offers strategies for prevention, covering:
- Common Causes of Item Master Match Exceptions
- Proactive Item Master Maintenance
- AI Vision Technology
Item master match exceptions at the point of use are caused by inconsistencies between the data listed for a specific product in the system and the coding of the product entered into the system by the Circulating Nurse. The data differences can happen for several reasons but the result is always the same – the data entry process falls down.
Item Master match exceptions appear on the screen when the nurse is either scanning, or entering surgical supply data into the system. These data differences can lead to significant challenges and delays for the circulating nurse. When the process becomes manual and offline, the quality and completeness of supply documentation can be compromised.
Common Causes of Item Master Match Exceptions
There are many reasons for data quality issues in perioperative documentation, including:
DATA QUALITY: Human error in entering data into the Item Master, or the data source of the Item Master, can lead to bad data and missed data.
DATA ENTRY ERRORS: Inputting errors by the nurse at the point of care mean that the product entered cannot find a match in the Item Master.
PRODUCT CHANGES: Changes in product specifications, packaging, or manufacturing can affect the Global Trade Item Number (GTIN) – the standardized, unique product identifier used for medical products. These changes may prompt a code update that is not yet reflected in the product’s hospital item master listing.
NEW PRODUCT: Substitutes, bill-only items, off-contract items, consignment etc. may not be listed in the Item Master at all, and will therefore not find a match in the system.
SOFTWARE GLITCHES: Errors in the Item Master software, or data migration errors, can lead to data errors or matching failures.
LACK OF STANDARDIZATION: It’s quite common for different departments to refer to products by different names. This can result in duplicate system entries, failed searches, and delayed administration.
Whatever the cause of the data quality issues, the perioperative documentation process breaks down, requiring additional time and effort to resolve.
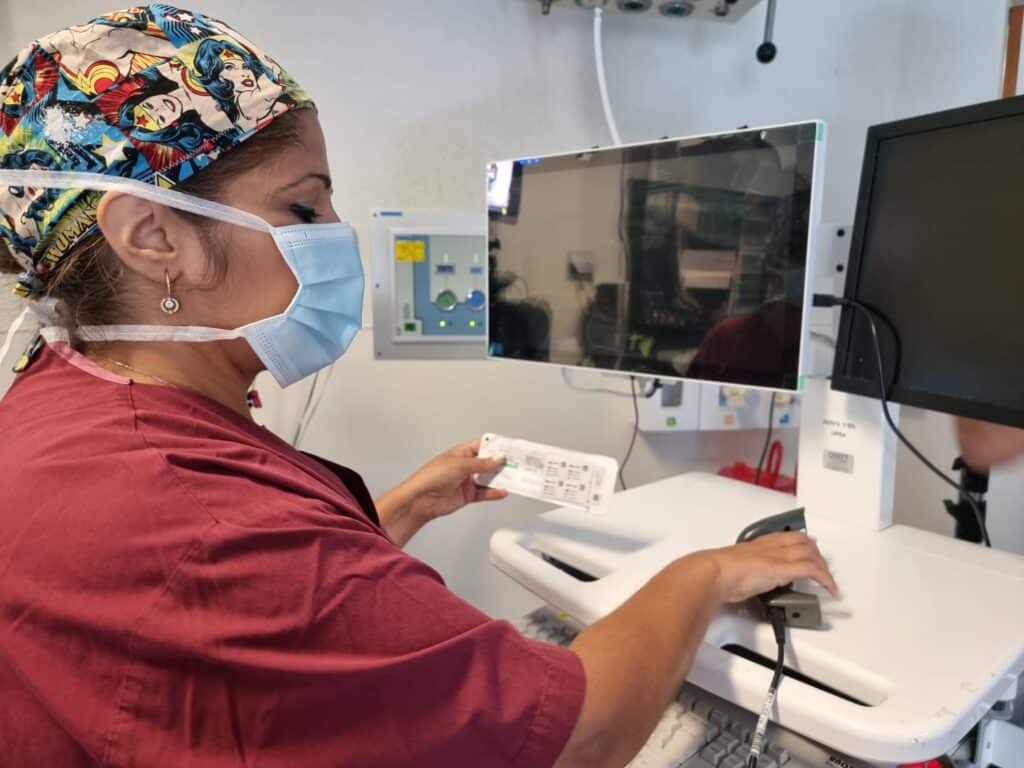
Preventing Item Master Match Exceptions
The best strategy for dealing with Item Master match exceptions isn’t to address them after they occur, it’s to prevent them from happening in the first place.
To improve the accuracy and efficiency of surgical supply documentation, organizations can implement new technology that not only captures the products used at the point of care, but also identifies the item and then verifies that all product data is complete and correct in the item master.
In the past hospitals took a reactive approach, with regular item master reviews being undertaken in an effort to keep on top of Item Master data. In reality Item Master maintenance is problematic since there are long periods between maintenance activity when the data in the Item Master becomes outdated.
A better approach is to be proactive and update the item master on the fly, every time new or altered product data is entered in the system. This perpetual Item Master update ensures every item is automatically identified and documented in the EHR – without the need for data entry or product research. This technology ensures standardized data is entered into the system and that the item master is continually maintained.
Automated Item Master matching software acts like a virtual Item Master by ensuring smooth documentation. This software takes care of data issues in the Item Master by ensuring any missing or incomplete data is updated.
By addressing Item Master listing discrepancies with AI technology, healthcare organizations can improve the accuracy and efficiency of surgical supply documentation, avoid item master maintenance costs, and enhance patient safety.
It’s time for healthcare providers to use technology that guarantees seamless point of use supply tracking while ensuring the hospital Item Master is always up to date and can recognize every item entered, either independently, or via the system’s cloud SKU data lake.
Kick Item Master match exceptions into the past. Find out about IDENTI’s AI Vision technology for seamless point of use surgical supply documentation, enabled by product data verification and correction software.