Medical Device Management
Item level management system to reduce implant waste & boost efficiency
Why implant tracking matters
High cost medical devices and implants put a strain on supply chain budgets which can represent up to 30% of US healthcare organizations’ expenditure. Yet poor management of this expensive inventory commonly results in high wastage, inflated costs, and revenue loss.
Providers commonly carry more than 25% excess stock and implant waste reduction results in millions of lost dollars each year. Invisible inventory carries a high price, and item-level tracking provides the solution.
What item level management delivers
Item level tracking involves individually monitoring and managing each item, so that full inventory visibility and control is achieved.
Gaining a clear understanding of the current inventory and using vital data insights to support better decisions, ensures cost, staffing and operational efficiencies, plus enhances patient-safety and compliance.
But item level data doesn’t just take care of the present, predictive analytics can be used for informed forecasting that drives through more precise planning.
Technology for medical device management
Automated implant tracking systems are able to achieve the real-time, accurate data required to successfully implement item-level management.
Automating inventory management supports more efficient management of both bought and consignment stock
Technology can now ensure precision tracking for every tagged item in your healthcare inventory, as well as the documentation of tagged and non-tagged items at the point of care.
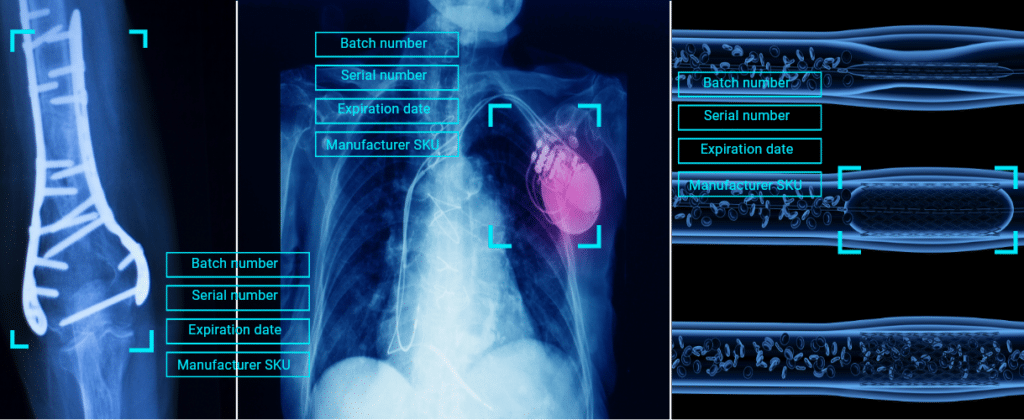
The three stages of item-level tracking
As medical inventory flows through the supply chain, there are three key stages of tracking that healthcare providers need to get right:
STOCK LEVELS: Clear inventory vision. Understand product volumes, locations and item level data, including full UDI.
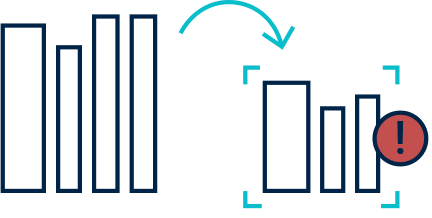
EXPIRATION DATES: Full control. Proactively manage expiry, ensuring all products are used rather than wasted.
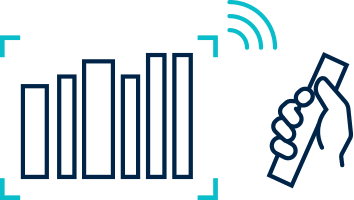
USAGE: Informed procurement. Gain surgical inventory control for demand-led restocks that eliminate obsolete stock.
Full visibility from supplier to consumption
Think RFID is inefficient? Think again! New generation UHF RFID technology is providing accurate healthcare inventory management and can also be used as a central system between supply chain partners, making it an ideal option for consignment.
With more sensors, and improved implant tracking, see how TotalSense smart cabinet uses RFID to closely monitor inventory.
TOTALSENSE RFID Smart Cabinet
Reorganize your surgical area using RAIN RFID smart cabinets.
Digital storage spaces fully track all items ensuring a well-managed and well-stocked inventory.
Ensure the right item is quickly at hand whenever you need it.

TOTALSENSE Mobile
Automate the management of tagged products stored on the shelves with our RFID mobile solution.
TotalSense Mobile transforms storerooms into digital storage spaces, creating a virtual smart cabinet.
Scan and review inventory data directly from your mobile phone.
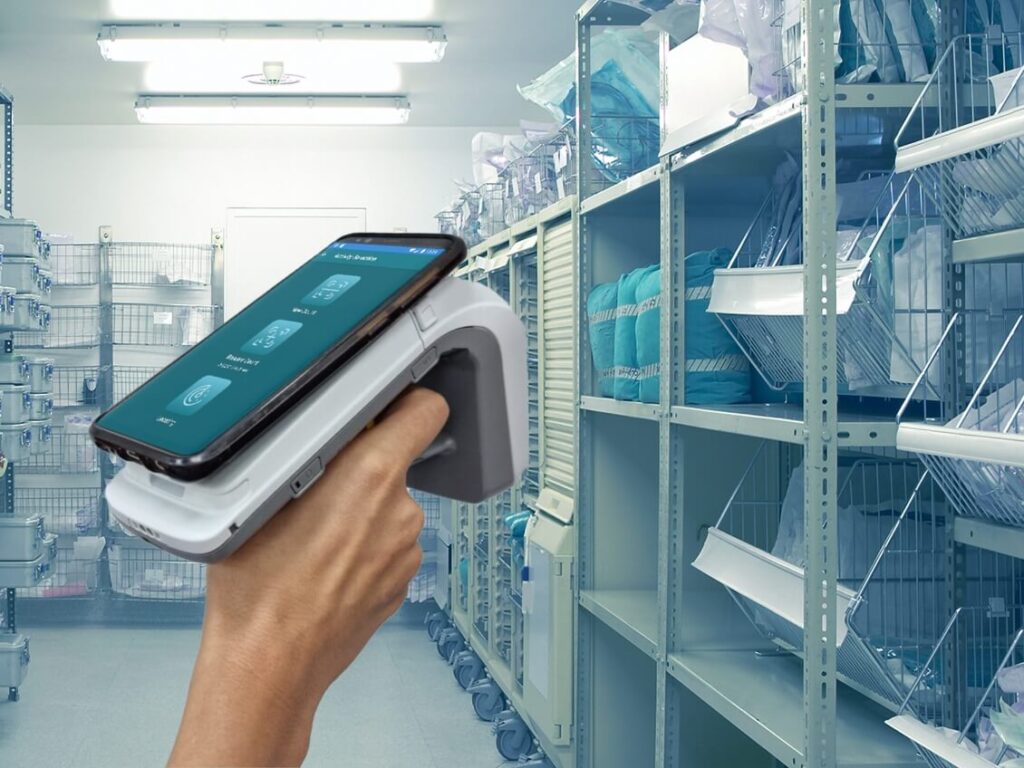
UDI compliance solution for surgical procedures – using AI and computer vision.
Put an end to UDI capture challenges in surgical supply documentation and enhance your medical device management in OR and procedural areas.
Existing point of use systems are inadequate and routinely result in incomplete and non-compliant patient records. Snap&Go uses image recognition and AI technology to capture full product information at the point of use, including SKU, batch number, serial/lot, expiry date and more.
Snap & Go is custom-made for the surgical setting and uses patented image recognition and AI technology. This automated implant tracking system for healthcare fully automates the task of surgical utilization, delivering complete and correct EHR records that include full UDI compliance in surgery, of every reportable implant.
Access to a globally populated SKU database ensures every item is validated, whether it’s listed on your local item master – or not.
AI technology and machine learning algorithms undertake UDI data-fixing and gap-filling, so that every item has a complete, correct, and standardized entry.

Recalls – quickly discover which patients have been effected by a product or batch recall.
Bring expiry wastage down to 0!
Compliance – ensure audit-proof documentation and full UDI compliance
Improve charge capture and achieve demand-driven procurement
Reduce admin – Release nurses from time-consuming data-entry with a fully automated process. Lower nurse docuentation time by 3–40%!