Consignment Stock Management
Supply chain partnership optimization – use AI to gain joint vision for smoother consignment management
Shared Data: The Key to Dispute-Free Consignment Stock Management
The consignment inventory management model is becoming more popular, but this “pay-per-use”, vendor-managed inventory (VMI) often causes delays and disagreements.
The problem is the lack of clarity over inventory that’s owned by the vendor or distributor, but located at the healthcare facility.
This disconnect causes uncertainty: What are the up to date stock levels? Which items were wasted? Which items were used?
Constant data discrepancies between supply chain partners trigger emails, faxes and calls, draining staff time and putting a strain on working relationships.
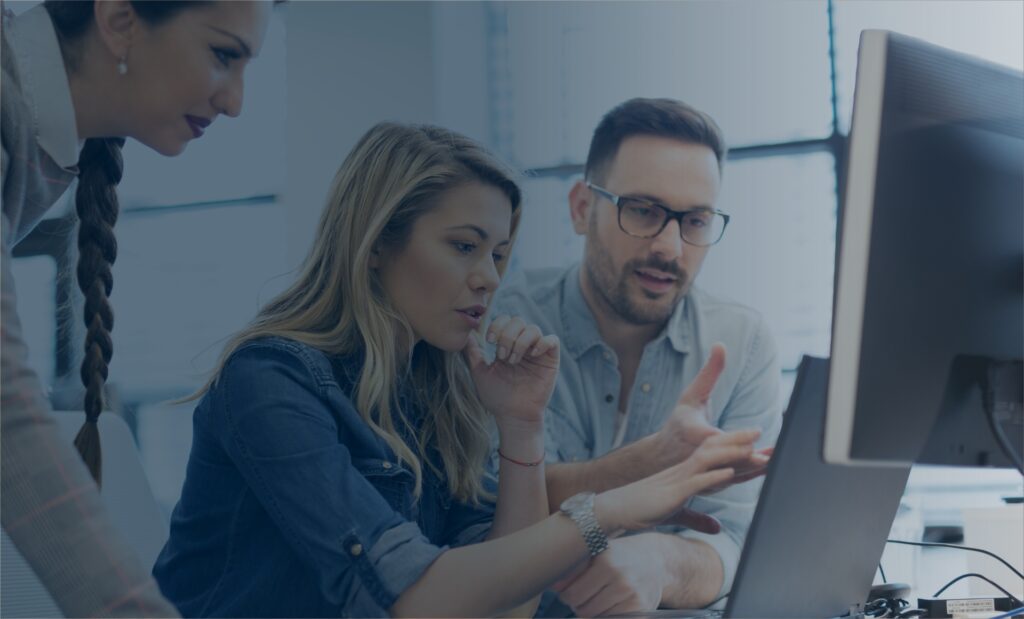
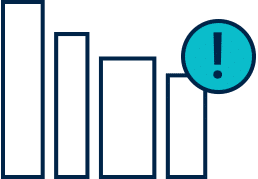
Inefficient manual processes and the use of separate inventory management systems lead to confusion over stock levels.
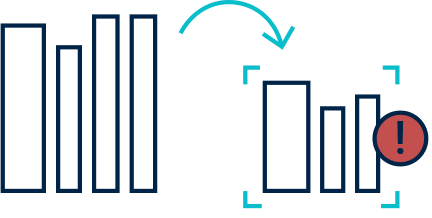
Off-site stock management by vendors/distributors hampers inventory vision and is a barrier to timely restocks.
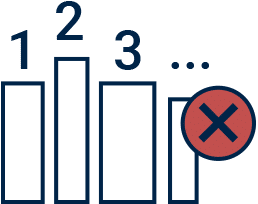
Lack of prompt usage data results in disagreement over consumption figures and delays billing.
Healthcare Consignment Management Solution
The only answer to consignment conflicts is for everyone to have shared vision.
It’s time to leverage technology to provide real-time inventory visibility for consignment management partners.
TotalSense is a UHF RFID smart cabinet, powered by AI cloud technology, that provides automated tracking and real-time visibility for ALL supply chain partners. This implant tracking system ensures everyone is in complete agreement on inventory data.
When everyone’s on the same page all parties can benefit from full inventory vision, timely restocks, and automated expiry management, enhancing performance and putting an end to disputes.
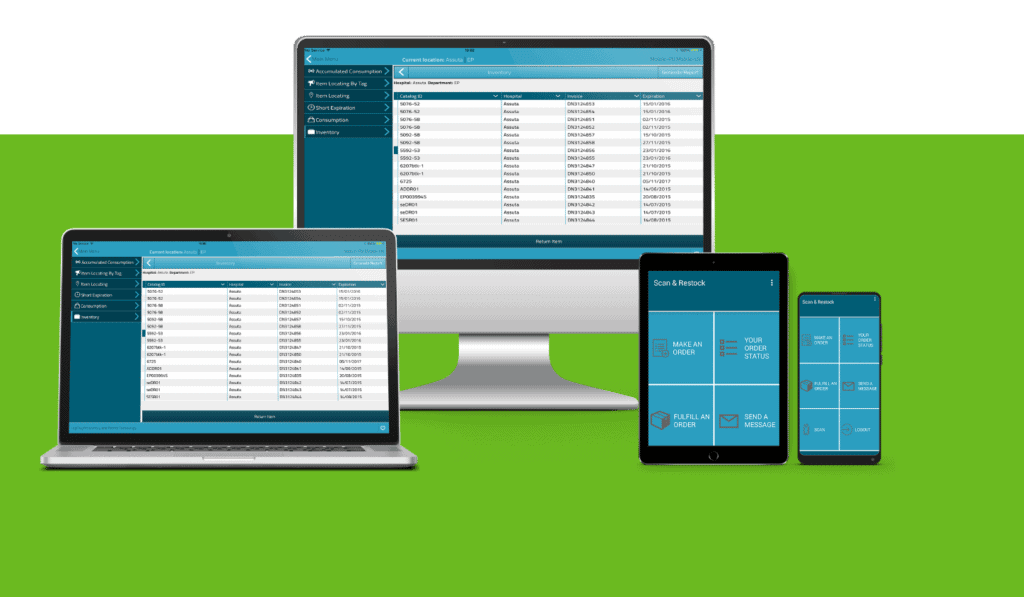
INVENTORY VISIBILITY
When vendors gain real time and enterprise-wide stock vision and usage data, they can reduce labor while improving data accuracy.
ITEM-LEVEL TRACKING
When products are managed at the item-level, automated, demand-driven procurement ensures the right stock is always at hand.
INVENTORY DATA
When there’s a single source of data consignment administration flows seamlessly and partner relationships are strong.
Three Routes to Successful Healthcare Consignment Management:
RFID Consignment Solution
Smart healthcare organizations are using technology to improve consignment management.
TotalSense smart cabinet is an automated consignment stock management solution that provides visibility across the entire supply chain. This eliminates discrepancies in data, ensuring all parties have a consistent understanding of stock levels. Achieving inventory transparency results in timely restocks and automated expiry management, minimizing waste and boosting patient safety.
With TotalSense all supply chain partners are on the same page, ensuring smooth, stress-free consignment management.
TOTALSENSE
RFID delivers full inventory transparency
UHF RFID Cabinet and Mobile Hand Scanner – for the management of tagged medical devices, tissue and implants.
- Real-time, item-level visibility and control.
- Access to a global product identification platform.
- Digital, UDI-compliant stock records.
- Effective expiry management.
- Automated, data-driven restocks.
- Inventory metrics, reports and insights
Perpetual stock monitoring keeps all supply chain partners up to date with real-time inventory levels, ensuring an optimized inventory, where all items are at hand when needed. In addition, dynamic data supports more informed implant management, providing insights that support smarter decision-making.
The image-to-data revolution
SNAP&GO gives perioperative teams superpowers! The innovative image-capture technology delivers full digital charting in OR and Procedure Rooms – using patent-protected image-capture technology.
Currently, all existing solutions on the market depend on scanning technology, (barcode/RFID/QR code), or necessitate manual data entry within EHR software. If an item is absent from the item master, nurses encounter difficulty completing reports as they receive error messages at the point of use.
Through a blend of digital image processing technology, which decodes images of items, and verification via a global SKU database, it’s now possible to routinely record items not listed in the Item Master, or that have an out of date listing.
Snap&Go simplifies consignment documentation at the point of use, with AI-driven automation reducing item and charge capture down to just three-seconds.